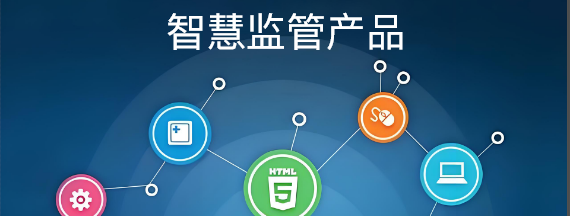
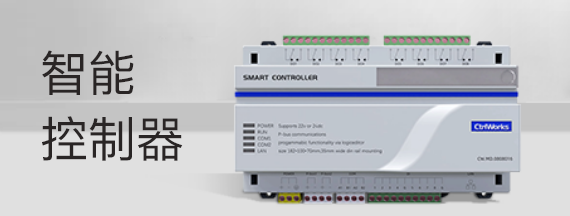
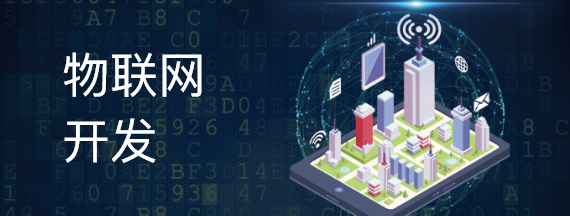
摘要:油源系统作为风洞的动力系统,在风洞的运行和测试中发挥着重要作用。由于长期处于高油高腐蚀环境,其各种部件和机构极易老化;风洞是我国主要生产风洞。它任务繁重,功能要求高。原油源头控制系统陈旧,故障频繁,维护工作复杂耗时。源代码控制系统的重新设计尤为重要;针对这种情况,设计了基于PLC控制的风洞油源控制系统,包括系统硬件设计、下位机PLC软件设计和人机界面设计等,全面部署在风洞中。在测控室和风洞现场,风洞油源系统的启停控制、油压无级调节、油冷却控制、状态监测等控制功能和操作方法油源系统,实现就地/远程控制。具有高度自动化、状态监控和功能扩展能力。
关键词:PLC控制机械电力系统油源系统风洞
风洞是航空航天领域极为重要的地面测试设施。油源系统是风洞的动力系统,为风洞中的所有阀门和执行器提供液压动力,用于实现各种困难状态下的自动测试模型。驱动和控制是非常重要的部件。本文风洞是我国主要的生产型风洞。控制系统非常陈旧,故障频繁发生。另外,随着国内对各种新设备的吹炼试验,风洞的运行性能和功能要求的进一步提高,原有的控制系统已经不是很好。以满足测试需要。尤其是油源控制系统,长期处于高油、高腐蚀环境中,各种部件和机构更容易老化,各种部件、机构和油品大多封闭在套管和管道中。这项工作既费时又困难。因此,对风洞油源控制系统进行重新设计,彻底解决油源控制系统老化、功能缺陷、设备停机等问题显得尤为重要。
可编程逻辑控制器 (PLC) 专为工业环境应用而设计。能够可靠稳定地完成极其复杂的控制任务,应用广泛[1]。 PLC经过多年的发展,已经形成了完整的系列工业产品。在功能和技术指标上,已经达到了软硬件成熟的水平。在风洞安全可靠运行的前提下,基于GEPLC控制,研制成功风洞油源控制系统,实现了油源启停控制、压力无级调节、状态监测、安全可靠、配置灵活、扩展性强。
1、油源控制系统原理
油源控制系统包括三部分:油源控制系统硬件部分、油源控制系统PLC软件和油源控制系统上位机软件。油源控制系统硬件包括测控室主站和测控室从站1、1#~4#油源控制柜和密闭控制箱等。整个油源控制系统是基于PLC控制,采用主从可编程逻辑控制器网络。测控室主站是整个系统的主站。主站作为从站,有一个CPU模块,从站提供与风洞现场设备的接口和主站的通讯,每个从站相互独立。监控室配备PLC主站和从站1、1#~4#油源控制柜和密闭控制箱作为5个从站布置在风洞现场。油源控制系统示意图如图1所示。
如图1所示,1#~4#油源控制柜的功能模块包括电机启停控制、压力控制、状态监测和安全联锁等。气密控制的功能模块箱体包括密封控制、压力监测等。1#~4#油源控制柜和气密控制箱通过总线[2,3]与测控之间的PLC主站通讯,实现监控整个油源状态和执行器的远程控制。 PLC主站通过总线模块与风洞测控系统中的其他系统进行通讯; PLC主站通过EGD总线模块与试运行管理计算机通讯,完成油源启停控制、压力调节、状态监测等功能。油源控制系统是软件和硬件的结合。全面部署在测控室和风洞现场,实现风洞油源系统和气密系统的自动控制,以及各种状态信息检测功能[4]。
图1风洞油源控制系统架构
2、油源控制系统硬件设计
油源控制系统的硬件设备是整个控制系统的运行载体,主要包括测控室主站、1#~4#油源控制柜、气密控制箱及通讯网络建设。油源分为4套(1#~4#油源),每个油源的硬件控制系统在相应位置布置4个机柜,即1#~4#油源控制柜,同气封控制箱位于密闭室内,每个系统都是一个独立的子系统(PLC从机)。
2.1 测控室PLC主站设计
测控室PLC主站是整个系统的主控单元,硬件资源配置为电源模块、CPU模块、通讯模块(主站模块、EGD总线以太网模块、总线控制模块)等。电源模块用于供电,CPU模块可以进行计算处理和通讯处理,通讯模块用于与各个从站通讯。
由国际组织提出,是基于工业以太网技术的新一代自动化总线标准。采用测控室主站与风洞各从站的连接方式,通过图形化组态实现通讯组态,简化了系统组态和调试过程。 EGD以太网模块,基于UDP/IP协议,实现设备间简单、高速、周期性的数据通信。该总线既是 I/O 总线又是通信网络,非常适合大规模 I/O 处理和数据传输。
2.2 PLC从站设计
PLC从站主要由1#~4油源控制柜和气密控制箱组成。 1#~4#油源控制柜作为PLC控制系统的从站,功能类似。油压调节、油源状态监测等功能;气密控制箱主要实现各部件的气密控制、气密状态监测、压力状态监测等功能。油源控制柜的硬件组成与密闭控制箱类似,主要包括总线模块、DI模块、DO模块、AI模块、AO模块、背板电源模块、开关电源、线性电源等。以1#油源控制柜为例,控制柜硬件设计框图如图2所示。
如图2所示,总线模块用于实现测控之间与PLC主站的通讯,接受主站的指令并传输数据。 DI模块、DO模块、AI模块和AO模块提供从站与现场设备之间的接口,是主站CPU与现场设备之间的桥梁。此外,每个油源控制柜均配备触摸屏(HMI),用户可进行就地控制和状态监控,实现远程/就地两种控制方式。密闭控制箱的硬件设计原理与此一致。 DI模块接收的主要信号有电源状态、门封状态、测试段密封状态和二进制段密封状态等。DO模块输出门封控制命令和测试段密封控制命令。 、二进制分段封口控制指令、异常故障报警。
图21#油源控制柜硬件设计框图
油源控制柜内电气及电路设计方案如图3所示。
油源控制柜内的电缆主要有6种,分别是380V交流电源线、220V交流电源线、光纤、以太网线、24V开关电源线、24V线性电源线和信号屏蔽线,1#油源控制 机柜与外接电缆的连接包括1#配电柜、高低压循环驱动电机、压力表、人机界面、比例溢流阀等资源配置及电气设计1#~4#油源控制柜中类似,不再详述。油源控制柜设计完成后,需要对各个IO模块的资源通道进行配置,主要包括分配地址、PLC程序中对应的变量名、通道的物理含义等。资源通道配置完成后,即可进行PLC软件设计。
2.3 通信网络建设
油源控制系统具有通讯设备多、通讯方式多样的特点(触摸屏采用以太网,PLC主从站采用),油源现场距离较远从测控室(电缆敷设长度)。最长近百米),如果使用纯网线,极有可能出现信号传输干扰的问题。此外,总线协议[5]与标准以太网总线协议的兼容性较差。如果使用同一个网络来传输上述两条总线协议信息,很容易造成网络拥塞和设备断线。为保证系统各设备之间稳定可靠的通讯,油源控制系统的通讯网络结构采用光纤环网(通过总线协议传输控制指令和油源状态信息)+星形网络(通过以太网协议完成触摸屏和PLC主站)CPU、测试管理和计算机之间的通信[4])相结合。总线通讯网络与标准以太网总线通讯网络隔离,保证油源控制系统网络的稳定性和可靠性。油源控制系统网络通信架构图如图4所示。
图3 控制柜内电气及电路设计
2.4 油温监测及电源压力控制
为实现温度监测功能,在1#~4#油源控制柜中各安装一个久茂电流输出型(4mA~20mA)/10-402型温度变送器,完成温度采集。温度变送器由油源控制柜内配置的24V线性电源供电,输出信号通过屏蔽线连接到控制柜内的AI模块端子。系统中的其余压力和液位传感器以相同的方式连接到系统。油源系统的温度监控兼具本地和远程监控功能,因此通过AI模块采集温度传感器信号并数字化,然后将双指针圆盘温度计安装在油箱显示面板上,实现本地温度显示功能,使用油源系统。控制柜内的触摸屏软件、测控室的实验运行管理、上位机软件实现远程温度监控功能。
油源系统的压力调节由电控比例溢流阀完成,根据输入的电信号连续按比例控制液压系统流体流量,避免油源冲击大的缺点。 “增压/卸荷”过程,确保油源“增压/卸荷”的无限精准调节。设计选用力士乐7X/型电控比例溢流阀作为调压的核心部件。
2.5 系统电源
油源控制系统的外接电源包括:测控室的电源面板和油源现场配电柜的电源()。测控室电源板提供的电源为不间断电源。为避免油源控制系统各控制柜(箱)内PLC设备意外断电,采用测控室电源板提供的不间断电源为PLC主站和PLC主站供电。每个从站。每个控制柜中的其他设备由风洞现场配电柜供电。油源风洞现场配电柜只提供电源,控制柜内的控制电源由电压转换后的隔离变压器(施耐德)提供。系统供电方案原理框图如图5所示。
图4油源控制系统网络通信架构图
3、油源控制系统软件设计
油源控制系统软件包括PC软件、PLC软件和HMI软件。主要功能是结合PLC等相关硬件设备,实现油源机组、泵组的启停控制、调压控制和油冷控制,同时完成液位等信号的监控传感器、温度传感器和压力传感器楼宇自控电磁水阀接线,以及相关数据和图形曲线显示等功能。具体软件功能如下:
1)本地/远程切换、电机状态、油位、油温、油压、滤清器堵塞变送器等状态监测;
2)根据本地/远程切换实现油源系统控制本地和远程切换功能,方便系统调试和维护;
3)实时监控软启动器的输出状态和油泵的状态。当出现异常时,会发出报警信息和信号,通知相关人员处理故障并采取相应措施;
4)实时监控油源系统的温度和液位。温度过高时启动循环冷却系统,冷却油源温度,液位过低时发出报警信号。 ,当出现极低液位时,可停泵,关闭阀门,保证系统安全;
5)实时监控油源压力和过滤器状态。当油源压力超过设定的正常值时,会发出报警信号,通知相关人员及时处理故障。当过滤器堵塞时,会发出报警信号。报警并通知相关人员及时更换新过滤器;
6)油源系统控制的主要对象有比例溢流阀、报警灯、空气阀,以及输出给联锁系统的系统工作状态信号;
7)根据系统启停信号实现油泵启停;
8)根据油源设定的工作压力值调节比例溢流阀,达到预定的油压值;
9)根据相应的报警状态激活报警灯,通知操作人员系统出现故障;
10)根据各油源子系统的工作状态,产生相应的输出给报警系统。
3.1个PLC软件
系统PLC软件包括PLC主站控制程序、1#~4#油源PLC控制软件和密封系统PLC控制软件。设计者采用并行化、模块化的软件开发思想完成PLC软件开发,保证PLC软件高效稳定运行[6]。下面以1#油源为例,简述PLC控制软件的设计思路。
1#油源监控对象包括:1#电机、2#电机、3#电机、温控泵、电磁水阀、比例溢流阀等。1#油源监控对象包括:1#油泵油压力、2#油泵油压、3#油泵油压、油位、油温等。结合风洞运行方式综合考虑,有3种控制方式:控制台远程、上位机软件远程和触摸屏软件本地控制。每种控制模式对应多种操作模式。例如可以启动(停止)1#油源。分为:单电机启动、升压、停止单独控制和单电机或2电机(1#和2#、1#和3#)一键启动和升压(降压和停止)两种方式。最终,1#油源运行控制模式多达38种,每种模式对应一套控制流程。下面以1#油源1#电机启动控制为例,说明相应的控制流程。限于篇幅,部分PLC控制软件不再详述。
1#油源1#电机单独启动的操作方式为:1#油源控制柜切换到远程模式,在触摸屏软件中点击启动1#电机按钮。由于循环泵和电磁水阀的控制比较简单,不需要单独配置控制流程,所以结合1#电机启动控制流程,1#油源2#电机,1#油源3#电机分别启动控制过程 过程同1#油源1#电机。其他如一键启动和升压等,不再赘述。
图5油源控制系统供电方案示意图
图61#油源1#电机启动控制流程
3.2 电脑软件
上位机软件由软件平台开发。 OPC服务器是通过软件附带的DSC软件模块建立的,PLC中的监控点必然实现上位机和下位机之间的通讯。上位机功能主要包括操作与显示屏、参数设置与存储、参数状态显示、历史数据记录、实时报警功能等。
1)系统权限管理:设置账号和密码,分别实现控制参数修改的操作和管理权限。
2)操作及显示画面:以现场油源使用情况为模板,设计动作操作过程的等效结构布局及显示画面,参数状态、数值及动作过程相关屏幕上显示相应的机制信号,直观的图像显示了注意力对象和场景的运行过程。根据每个对象的动作控制,在屏幕上设置相应的操作按钮,并在它们之间关联下位机PLC程序中的动作控制。
3)参数设置与存储:包括油源控制系统的控制执行指令和辅助参数设置功能,可实现参数在本地上位机和下位PLC的双重存储;
4)历史数据记录:将油源控制系统的控制命令参数、监控状态参数、控制辅助参数、运行画面参数等记录在历史数据库中;
5)实时报警功能:实时显示油源控制系统下位PLC发出的报警信号。
本系统开发的上位机软件操作界面图如图7所示(以1#油源为例)。
图7 PC操作界面-1#油源
4、结束语
以GEPLC作为油源控制系统的控制模块,利用软件平台开发上位机软件,设计了一套风洞油源控制系统,实现了风的启停控制。隧道油源系统、压力无级调节、油冷控制、油源系统状态监测、本地/远程控制等功能。该控制系统已投入使用,运行可靠、安全性高、扩展性强,完全可以满足风洞油源控制的应用要求。